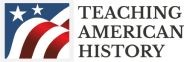
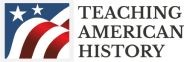
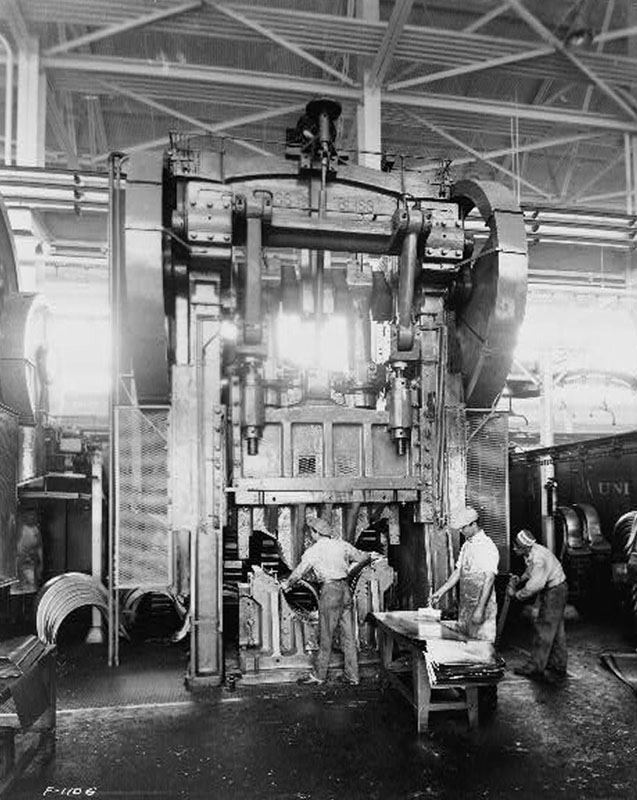
No related resources
Introduction
In 1908 industrialist Henry Ford (1863–1947) introduced the Model T, the “car for the great multitudes,” made affordable by Ford’s manufacturing innovations. To speed up production and reduce costs, Ford standardized parts and installed moving conveyor belts in his well-lit and ventilated factories. Assembly lines were efficient, but the work was tedious, and workers often quit after only a short time on the job.
In 1914 Ford made the stunning announcement that he was raising the minimum wage in his factories to five dollars a day (twice the standard industry rate) and implementing an eight-hour workday (ten to sixteen hour workdays were the norm). The move made business sense, he argued. Higher wages would reduce worker turnover, attract better workers, and create new customers for consumer goods like cars. Reducing daily work hours would lessen fatigue-induced mistakes, thereby raising worker productivity. Ford also hoped that the overall popularity of these measures would allow him to continue running his factories unencumbered by either unions or minimum wage and maximum hours laws.
The higher wages, however, came with conditions attached. The pay increase was initially a bonus of $2.70 added to the $2.30 daily base pay. To qualify, workers had to stay sober, contribute to a savings account, maintain a clean home, and refrain from domestic abuse. In 1921 Ford abandoned these requirements, which were nearly impossible to enforce. By then, he had raised the daily minimum wage in his factories to $6.
In 1922 Ford made headlines again when he announced a plan to introduce the five-day workweek, which he implemented in 1926. In the excerpts below, newspaper editorialists considered the merits of Ford’s proposal and his overall approach to management-worker relations.
Source: “Henry Ford’s Five-Day Week,” Literary Digest (April 29, 1922), 8. Available at https://babel.hathitrust.org/cgi/pt?id=mdp.39015028101460&view=1up&seq=406.
Will Henry Ford’s five-day week, with the minimum basic day-wage of $6 unchanged, benefit the Ford employee who has been working six days a week? True, he has an added day’s leisure for rest and recreation, or for self-improvement, but he also loses at least half a day’s pay. Will family and individual budgets have to be slashed because of the recent reduction in working days? These are some of the questions that occur to the Newark News, published in a manufacturing city. Ford announces that in order to provide employment for several thousand of Detroit’s idle workers, and to afford workers already on the payroll more time to spend with their families the Ford Motor Company and its allied interests will adopt, as a settled policy, the 40-hour week, the workers now in the service to continue to receive a minimum wage of $6 per day and new employees $5 per day. Dispatches from Detroit note that a minimum of $5 per day was the wage-scale established in 1914 by Henry Ford, and that it was during the war period that this was raised to $6 to enable employees to meet higher living costs.
“The Ford plan is joyous news to all who like to think of bringing work down to the irreducible minimum,” remarks the New York Herald; “later we shall have a thirty-hour week, then a twenty-hour week. Perfectly fascinating.”
Approximately 55,000 men, according to Edsel Ford,1 will be affected by the new order, while some 5,000 additional employees already have been taken on. The management, we are told, believes that with more leisure the workers will be more contented and that there will be a corresponding increase in efficiency. Certainly, as the Boston Financial News predicts, “the working out of this latter innovation will be watched with considerable interest, if not concern, by all other employers of large numbers of workmen.” A few editors recall the wide-spread scoffing, and the prediction that Ford would suffer financial collapse, upon his radical departure from common practice almost a decade ago. “Yet,” observes the Louisville Courier-Journal, “it was after he announced an astonishing and seemingly impractical wage-scale that he made his greatest success.” And, in the opinion of the New York Herald, Mr. Ford is just as canny now as he was in 1914. Says The Herald, in an editorial headed “Henry Ford’s Stroke of Genius”:
Henry Ford’s five-day week may be only another proof that his business genius blazes undimmed upon his own automobile industry, in which he is the world’s incomparable inventor, manufacturer, salesman and publicity agent.
It cannot be that Henry Ford has failed to discover, along with so many other employers, that the Saturday half-holiday wasn’t any good as half a work-day, anyhow. The workers report, ready to quit before they begin, with their eyes on the clock and their minds on what they are going to do after their midday release.
It cannot be that Henry Ford has failed to consider that even he, like other employers, couldn’t get half a day of work out of his men on Saturday for half a day of pay.
It cannot be that Henry Ford has failed to speculate on the very good chance that he, the man who is always speeding up production, can so speed it up further that he will get as many cars out of his 50,000 men working five days a week, with a correspondingly smaller pay-roll, as he before got out of them working five and one-half days a week.
Other employers couldn’t do it with their clerks, and possibly the average labor, for while such workers can speed down on Saturday forenoons, with their eyes and brains full of the half-holiday ahead of them, there is no Henry Ford dynamics to speed them up the other days. Henry Ford can.
Apparently organized labor is satisfied with the new arrangement, for Samuel Gompers, head of the American Federation of Labor,2 is quoted as saying that “Mr. Ford will find his new plan as beneficial as he found the introduction of the eight-hour day, both as to quality and quantity of output.” “Mr. Ford, in his recent announcement, shows that he fully understands the human element, or factor, in production,” agrees Matthew Woll, one of the vice-presidents of the American Federation. And as we read in the Pennsylvania Labor Herald, of Allentown:
In establishing the five-day workweek plan in his Detroit factories, Henry Ford again shows that he intends to maintain the most efficient shop force in the automobile industry. Instead of reducing working forces and disrupting his producing machine, Ford supplies his present needs by working his force five days per week and keeps his wages to the point where his employees can maintain a decent standard of living. This in turn keeps these men in a state of mind where the maximum production can be secured, and it is a question whether or not the production will not be increased per work-day, rather than decreased through the shorter week. Any manufacturer who treats his employees fairly will surely be well repaid, and Ford is entitled to anything he gets by trying to keep in mind that his employees are entitled to a decent living and that production in his plant will be maintained with that thought in mind.
“It is true,” admits the Boston Christian Science Monitor, “that Ford’s plan means that the pay envelop of the present employees, who are on a $6-a-day basis, will be found to contain only $60 each bi-weekly pay day, but it is also true that by stabilizing conditions in the city as a whole the new plan is almost bound to react upon living conditions favorably.” As this paper goes on to point out:
The almost unmeasured benefits which this action promises in relieving the unemployment situation in Detroit will offset, at least to some degree, any loss that might be felt by individuals, and even tho the new rate does mean a slightly decreased hourly wage, it must be remembered that cuts in wages are being made all through the country, and that the generally improved living conditions are enabling a family to live comfortably today on considerably less than a year or so ago.
“As to the five-day program in the abstract, it is obvious that it is better to have six men employed five days a week than five men six days, with the sixth out of work all the time,” believes the Newark News. And, notes the Boston Financial News:
The five-day week becomes all the more spectacular introduced, as it is, at a time when more work and longer hours, rather than less of either, is being advocated by the world’s leading economists and businessmen alike, not only as a panacea but as a requisite to the return of normal business and living costs. The contrast is specifically striking in the case of the textile industry, the operators of which assert that nothing short of more work at less pay will insure its survival. An added contrast may be found in certain phases of the steel and iron industry which apparently continues to require twelve-hour days and seven-day weeks.
“A generation ago, when the eight-hour day or 48-hour week movement got under way,” recalls the Cleveland Plain Dealer, published in a great industrial center, “there were numerous old fogies who predicted that the country would be ruined if the shorter week became general, but they have been proven false prophets.” Moreover—
If all the capitalists of the country followed the example of Henry Ford the 4,000,000 to 5,000,000 unemployed workers would be quickly absorbed, the work that is to be done would be spread over all industry, much human suffering and misery would disappear, and business would come back to “normalcy” in short order.
On the other hand, the Cleveland Commercial fears that the new Ford policy will create more unrest among the labor people of the country and cause them to ask for the same conditions. The Huntington (W. Va.) Advertiser also finds it “difficult to see that Ford’s present employees will derive any benefit from the new arrangement.” As this paper sees it—
They will receive wages for five days instead of six days. Their earning capacity has been reduced one-sixth. Doubtless most of them would consider one day out of seven sufficient for recreation and rest, and would prefer to work that sixth day instead of loafing and earning nothing.
- 1. Edsel Ford (1893–1943), Henry Ford’s only child, became president of the Ford Motor Company in 1919, although Henry Ford continued to direct the company behind the scenes.
- 2. Samuel Gompers (1850–1924) led the American Federation of Labor (AFL) from its founding in 1886 until his death. The nation’s largest union, the AFL was an association of craft-based unions whose membership consisted mostly of skilled, white, male workers.
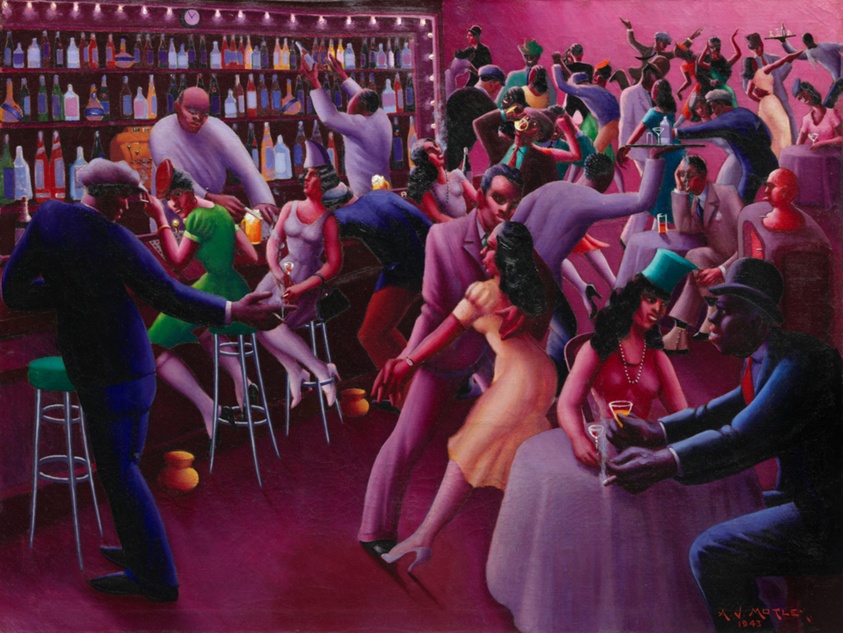
Conversation-based seminars for collegial PD, one-day and multi-day seminars, graduate credit seminars (MA degree), online and in-person.
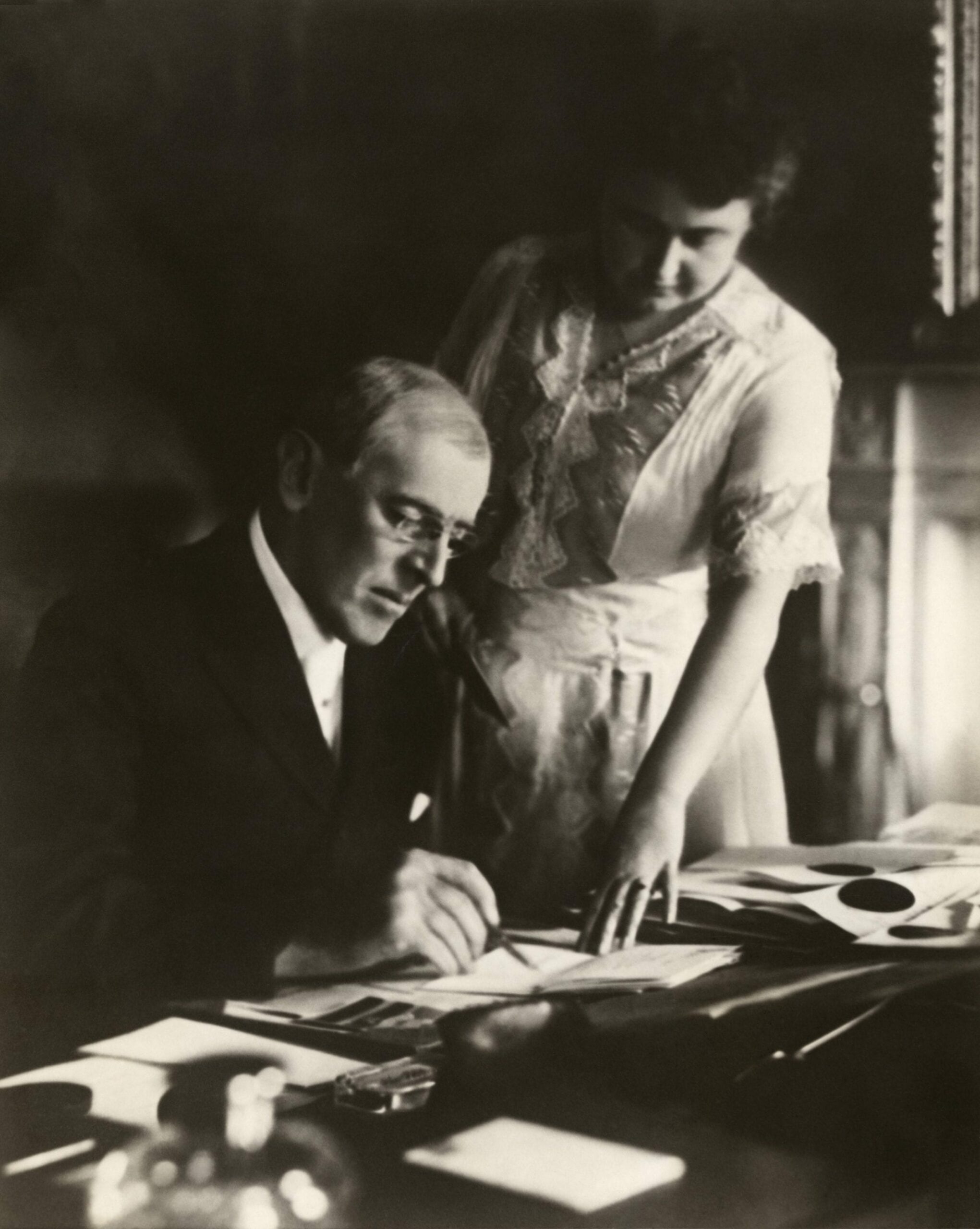